30 Dec 2024
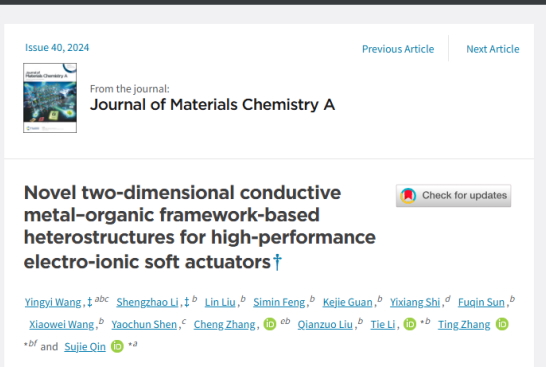
"In soft robotics, electroactive polymer (EAP) materials hold great promise due to their flexibility and adaptability, allowing them to perform effectively in complex, unstructured environments while ensuring safe interaction with humans," said Dr Sujie Qin from the Department of Health and Environmental Sciences.
Dr Qin further explained that ion polymer-metal composites (IPMCs), which consist of ion polymers and surface metal conductors, have emerged as an important category of EAP materials. They have attracted significant attention from researchers in the field of flexible actuators in recent years.
IPMCs operate on the principle that when exposed to an external electric field, the anions in the sandwich structure of the IPMC migrate towards electrodes, resulting in asymmetric volume changes. This leads to macroscopic mechanical deformation and actuator behaviour. However, common electrode materials for IPMC actuators, such as platinum and gold, often struggle to maintain electrolyte compatibility, high conductivity, and high capacitance during bending, which significantly limits actuator performance.
According to the PhD student Yingyi Wang, to address these limitations, the research team combined poly(3,4-ethylenedioxythiophene)-poly(styrenesulfonate) (PEDOT:PSS), a material with high conductivity and capacitance, with in-situ locally converted Zn0 nanorods to form Zn-CAT-based EC-MOF electrode materials. This innovation resolves several key challenges faced by traditional IPMC actuators, including insufficient conductivity and poor electrolyte compatibility during bending.
Experimental results have demonstrated the exceptional performance of the new actuator: an ultrafast response time of 1.56 seconds, low energy consumption (operating voltage between 0.1 and 5 volts), large bending strain (1.22%), and remarkable cycling stability (97% after 10,000 cycles). Furthermore, the composite material exhibited light-heat-electric effects when exposed to 700 nm light, increasing the bending strain to 2.38% and the output force to 66 mN.
These advancements are expected to drive the development of soft robots with applications in fields such as medical devices, rescue operations, environmental monitoring, and manufacturing.
Content: Dr Sujie Qin
Translator and Editor: Luyao
30 Dec 2024